課題解決事例
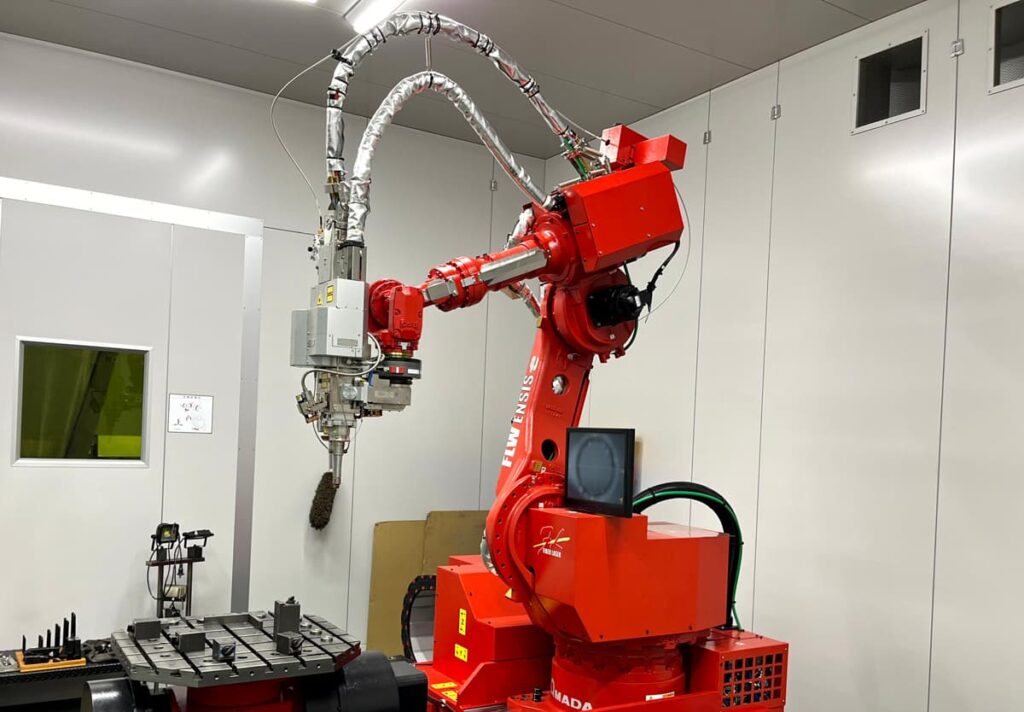
CASE 01
外装部品の歪み・外観品質改善及び工数削減によるコストダウン
お客様の課題
産業用設備の外装カバーにて、アーク溶接を使って外装カバーの製作指示をしていたが、溶接歪みが出てしまう為、組立にて干渉が発生してしまうとのご相談をいただきました。
加えて他社での製作には、溶接部品の位置決めにダボを使用していて、外観面のダボのへこみが埋まらず、塗装後にその部分が目立ってしまい、外観品質にお困りとのことでした。
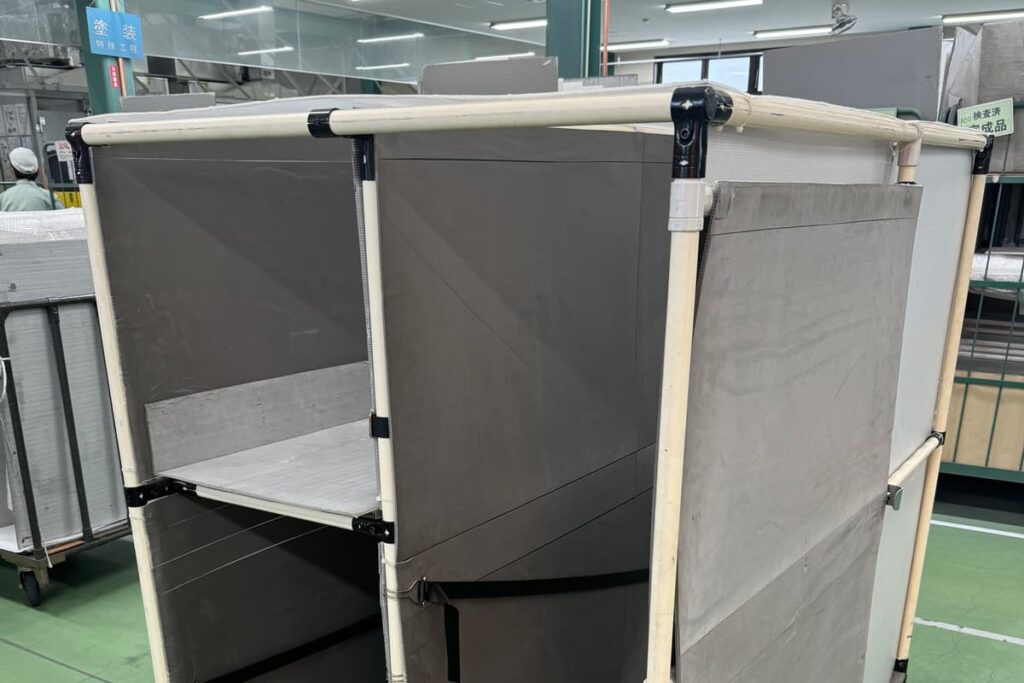
CASE 02
専用台車によるキッティング作業の時間短縮
お客様の課題
ダンボールやコンテナなどで納品された品物をキッティングする際、梱包を解くことによる手間がかかっていたり、誤って品物を傷つけて不良としてしまう恐れがあった。
とくにサイズの大きな品物や、外観品質が重要な品物に至っては、通常よりも慎重にキッティング行う必要があり、工数の増大につながっていた。
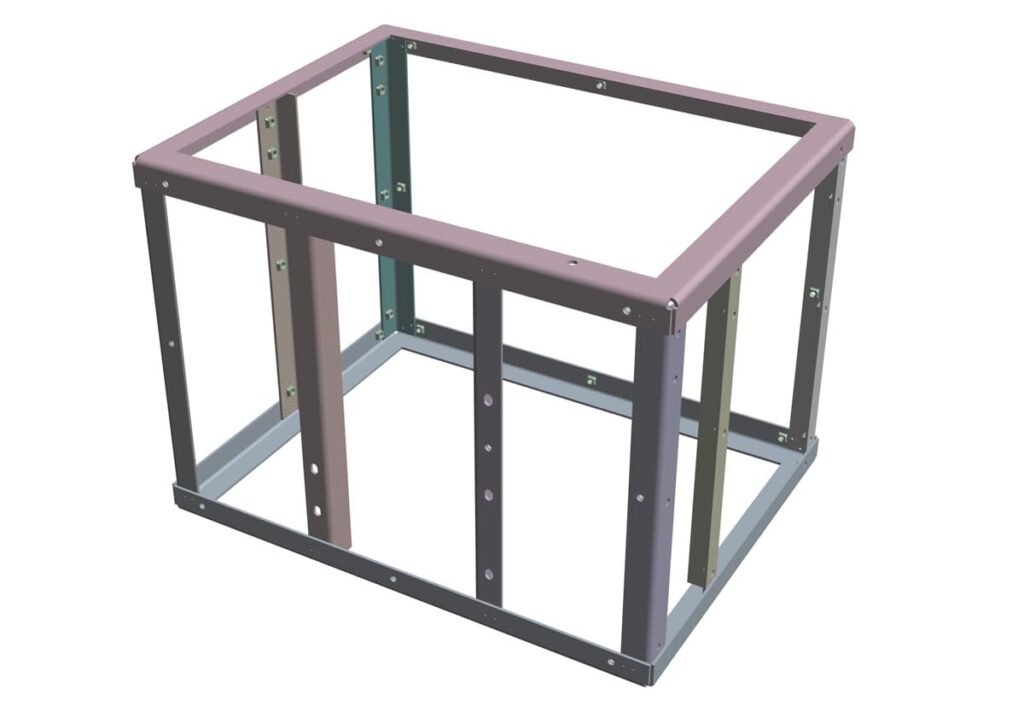
CASE 03
フレームの加工方法変更でコストダウンを実現
お客様の課題
お客様よりアングルを用いたフレームの製作のご相談とコストダウンが課題になっているとのご相談をいただいた。
アングル材を加工する為に、高精度な治具の設計・製作、切断・穴あけなどの作業が人的な作業となり、コストの増大、リードタイムがの長期化が課題となっており、これらを解決できないかとの内容だった。
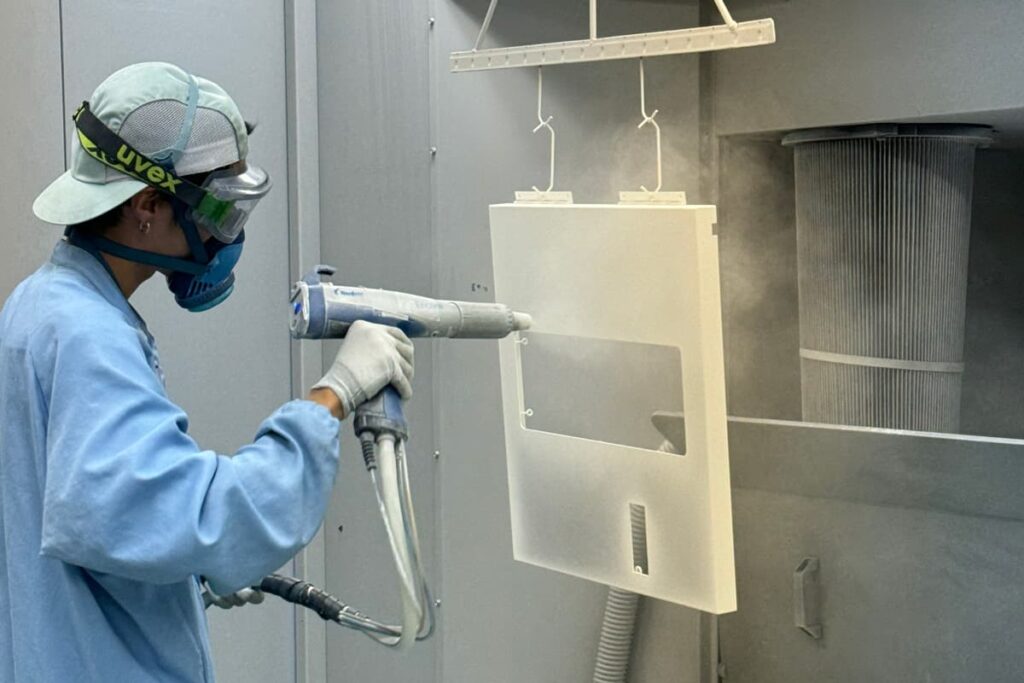
CASE 04
溶剤塗装から粉体塗装への変更でVOCを低減
お客様の課題
お客様より、近年の環境対応の一環として、外装部材の溶剤塗料の見直しのご相談があった。
溶剤塗料ではサテンの仕様をとされており、模様塗装かつ揮発性有機化合物(VOC)の低減を図ることができる。
人や環境にやさしい商品のための塗料への変更を希望とされていた。
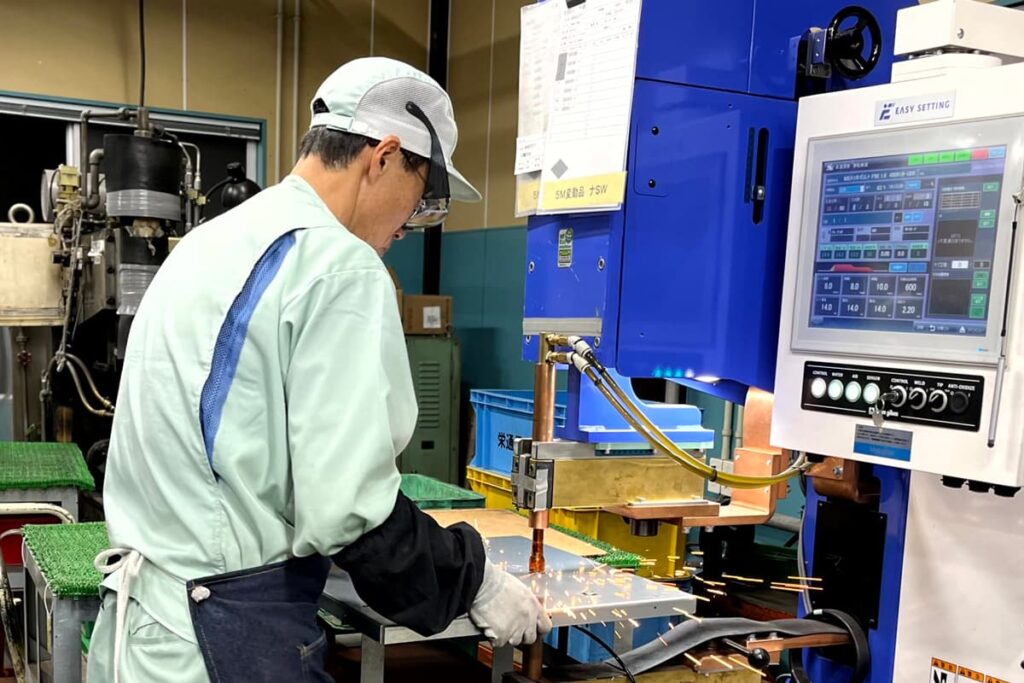
CASE 05
リベット組立と溶接併用によるコストダウン
お客様の課題
お客様より、従来製作をお任せいただいている品物の次期モデルの開発に際して、現行品の強度を落とさず、コストダウンを行いたいとの相談があった。
現行品は強度確保のため、全周溶接の指示があり、溶接工数も多いうえに歪みの修正にも工数がかかっていた。
溶接は表側からの全周溶接で、溶接部を平滑に仕上げる指示となっている。